Bamboo textile nowadays gains more and more popularity as an abundant source of the fashion industry. Many favor it for its friendliness to the environment and goodness for people.
We have written this article providing necessary detailed information for those still unfamiliar with this kind of fiber. Check it out now.
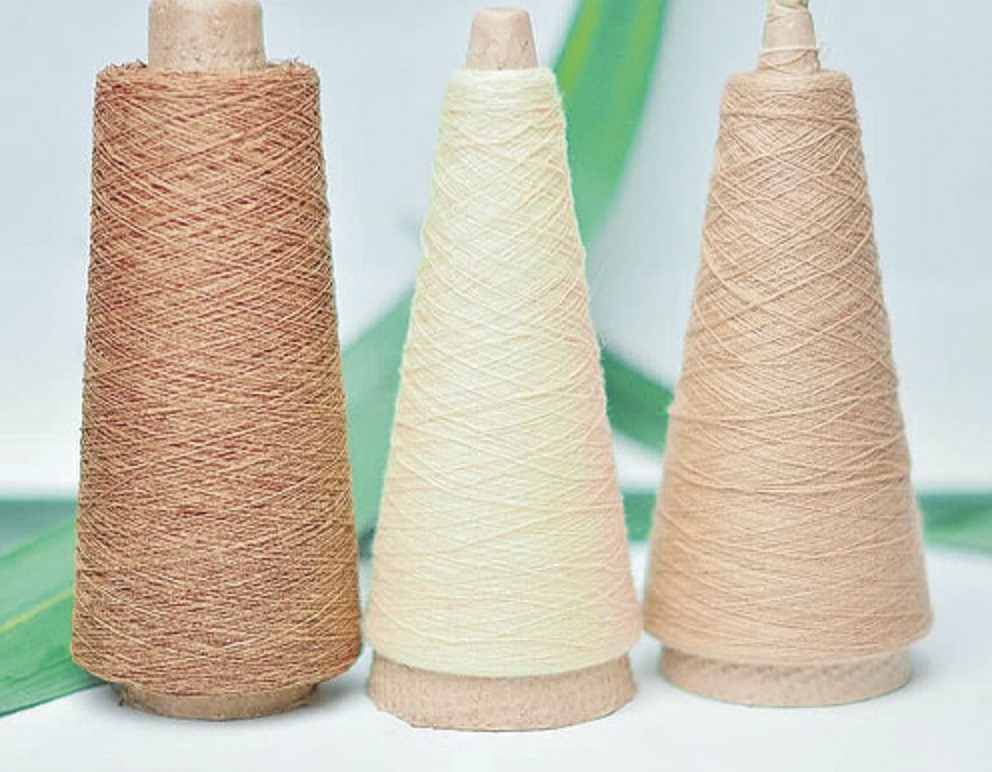
1. Different Forms Of Bamboo-derived Fiber
Bamboo textiles come in various forms, although they are all fabricated or extracted from natural bamboo. Here we get three typical kinds:
1.1. Stiff Strips
People widely use bamboo fiber in thin stiff strips for basketry, hats, or shoes. A popular example that you can see is bamboo hats that farmers and fishers wear to avoid the sun.
Moreover, you can find this form of bamboo in corsets, bustles, and other elements of women’s dresses.
1.2. Bamboo Rayon
When it comes to bamboo rayon, the production is more complicated than the previous one. It is a semi-synthetic fiber made from cellulose extraction.
Specifically, the manufacturer picks leaves and the soft, inner pitch from the bamboo trunk, puts them in steep, and mechanically crushes them.
They will create viscose rayon from above-extracted cellulose and treat the fibers through several chemical processes. After all, rayon is formed and used in making home furnishings.
1.3. Mechanically Produced Fine Bamboo Fiber
Another form of bamboo fiber comes into being through a mechanical-bacterial process. The mechanically crushed woody part of the bamboo undergoes the natural enzyme retting and washing procedure to extract the fiber. Then, the workers will spin this into yarn, which is sometimes called bamboo linen.
2. Advantages, Disadvantages, And Potential
Bamboo textiles do have some advantages and disadvantages. This type of fabric does not completely lean towards eco-apparel. Meanwhile, bamboo fibers do not ensure the warranty.
It is reasonable when labeling enforcement bodies ask to reduce the greenwash in those facilities of bamboo production.
2.1. Advantages
While considering the alternatives for bamboo textile, we must acknowledge that nothing is perfect.
For example, cotton comes in both conventional and organic versions, but its resource is water- and cultivation-intensive crops, which are more complicated and time-consuming to grow.
Besides, polyesters and acrylics need much energy, chemicals, and water to manufacture.
2.1. Disadvantages
Despite the advantages mentioned above, bamboo textile production, especially chemical technology, poses a risk to workers’ health if they cannot control the process well.
Specifically, utilized sodium hydroxide can make their skin and eyes irritated. Meanwhile, sulfuric acid and carbon disulfide somehow affect neural disorders and respiratory problems.
In addition, effluents from the bamboo textile procedure may damage the surrounding environment due to poor management.
2.3. Potential
Of course, there is a chance for bamboo fiber to promote its full potential. Nowadays, many cleaner production processes are appearing along with interest in the environmental attributes of this type of fabric.
Let us take an example. Some companies these days have applied the more benign chemical technology to make bamboo fibers. They take full advantage of manufacturing lyocell from wood cellulose to utilize bamboo cellulose.
Specifically, toxic chemicals are less, and a closed-loop system during the process can capture 99.5% of those chemicals and recycle them.
Further, labeling enforcement bodies pay much attention to the transparency of bamboo textiles. It will lead to advances in the environment and labor certifications of bamboo-based fabric manufacturing lines.
3. How Is Bamboo Textile Fiber Made?
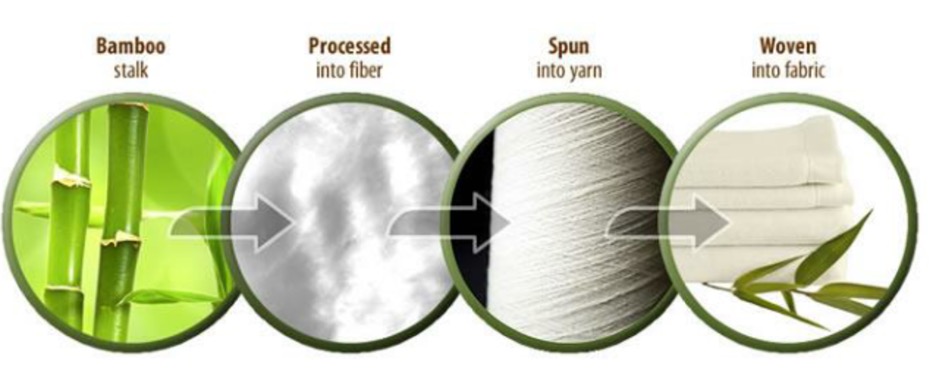
There are two typical ways to make bamboo textile fiber, including mechanically and chemically:
3.1. Mechanical Process
The mechanical process involves crushing the woody part of the bamboo into a pulp and then breaking the cell walls with natural enzymes.
After getting a mushy mass, the manufacturer will comb the material out mechanically and spin it into yarn. The fabric result is quite similar to linen, but this way costs lots of money and is labor-intensive, so it is not popular.
3.2. Chemical Method
Compared to the mechanical method, the chemical one is highly preferred. Let’s go into details.
Like the previous way, the workers crush the bamboo but soak it in a strong chemical solvent, called sodium hydroxide, at about 20-25 degrees C for 1-3 hours instead. This process will produce alkali cellulose, then they press the excess solution, crash it with a grinder and let the material dry.
After that, carbon disulfide is added to the bamboo alkali cellulose to create cellulose sodium xanthogenate through the process series of sulfurizing, and decompression.
A diluted sodium hydroxide, once again, is added to the above solution to form viscose cellulose. Then, the makers use a diluted sulfuric acid solution to harden the bamboo viscose into bamboo cellulose fiber threads.
You can spin these into yarn for weaving into a soft and highly absorbent bamboo fabric.
4. Bamboo Labeling: “Rayon From Bamboo.”
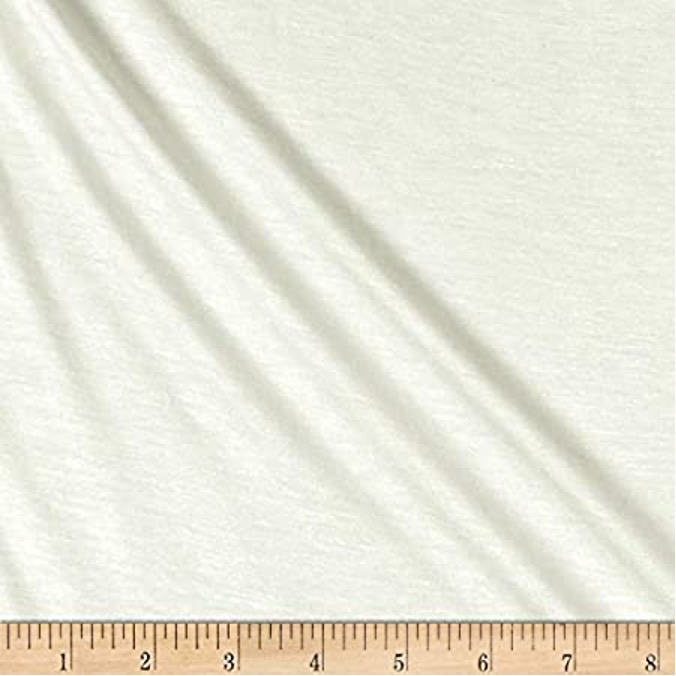
When more and more companies introduce their bamboo textiles as super-eco and awesome products, some councils tend to ask for strictly checking this labeling.
To be more specific, both the United States Federal Trade Commission and the Competition Bureau of Canada have kept labeling textile articles from bamboo under control. This results in requiring the bamboo textiles to be labeled specifically depending on their chemical process.
For example, “Rayon from Bamboo” is completely different from simply “bamboo.” What is more, the manufacturer must mention the performance and environmental claims, such as “biodegradable ” or “naturally antimicrobial.”
It allows consumers to not get wrong on the unsubstantiated “green” claims while choosing clothing and textile items. Any act of deceptive labeling and advertising items must not be recommendable. And these sellers may pay a fine for this reason as well.
5. Bamboo Textile Certification
Bamboo textile certification is put into practice in many factories to relieve the environmental and worker safety concerns. Lots of textile certification schemes are available, yet the Oeko Tex Standard 100 is the typical one.
It confirms that the finished fiber is eco-friendly and safe without harmful chemicals. However it is worth considering that this standard only considers and assesses the outcome instead of the chemical usage throughout the textile production.
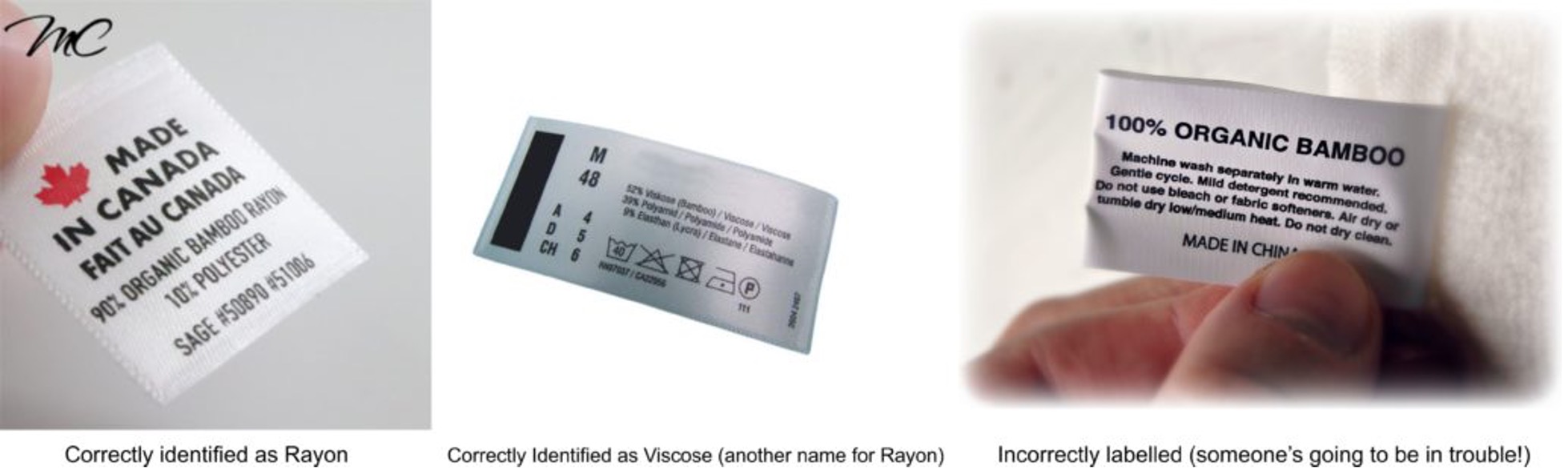
Similarly, there are several factory certification schemes, including ISO 14001 and the SA 8000 program. The ISO standard points out that the factory has applied the environmental management system to green their procedures.
On the other hand, the SA certification defines the social accountability side, yet not the environmental one. Of course, both standards aim at business-to-business use, not the consumer. That’s why some consumers will find it hard to determine whether a bamboo garment comes from a guaranteed facility or not.
To Sum Up
We believe that you have broadened your knowledge of bamboo textiles after consulting our in-depth article above. It is no doubt a sustainable yet renewable resource that many manufacturers of apparel highly praise to utilize.
Further, this fabric is worth adding to your favorite list of soft, safe, and eco-friendly textiles. However, you should still be smarter while choosing the suitable type used in the clothes. Good luck!https://wikibamboo.com
Help Us! Share on: